Siamo consulenti per lo sviluppo.
Acceleriamo lo sviluppo aziendale attraverso interventi di trasformazione digitale e consulenza in finanza agevolata.
Chi siamo?
Siamo consulenti specializzati in innovazione digitale e finanza agevolata. Due anime dedicate allo sviluppo aziendale.
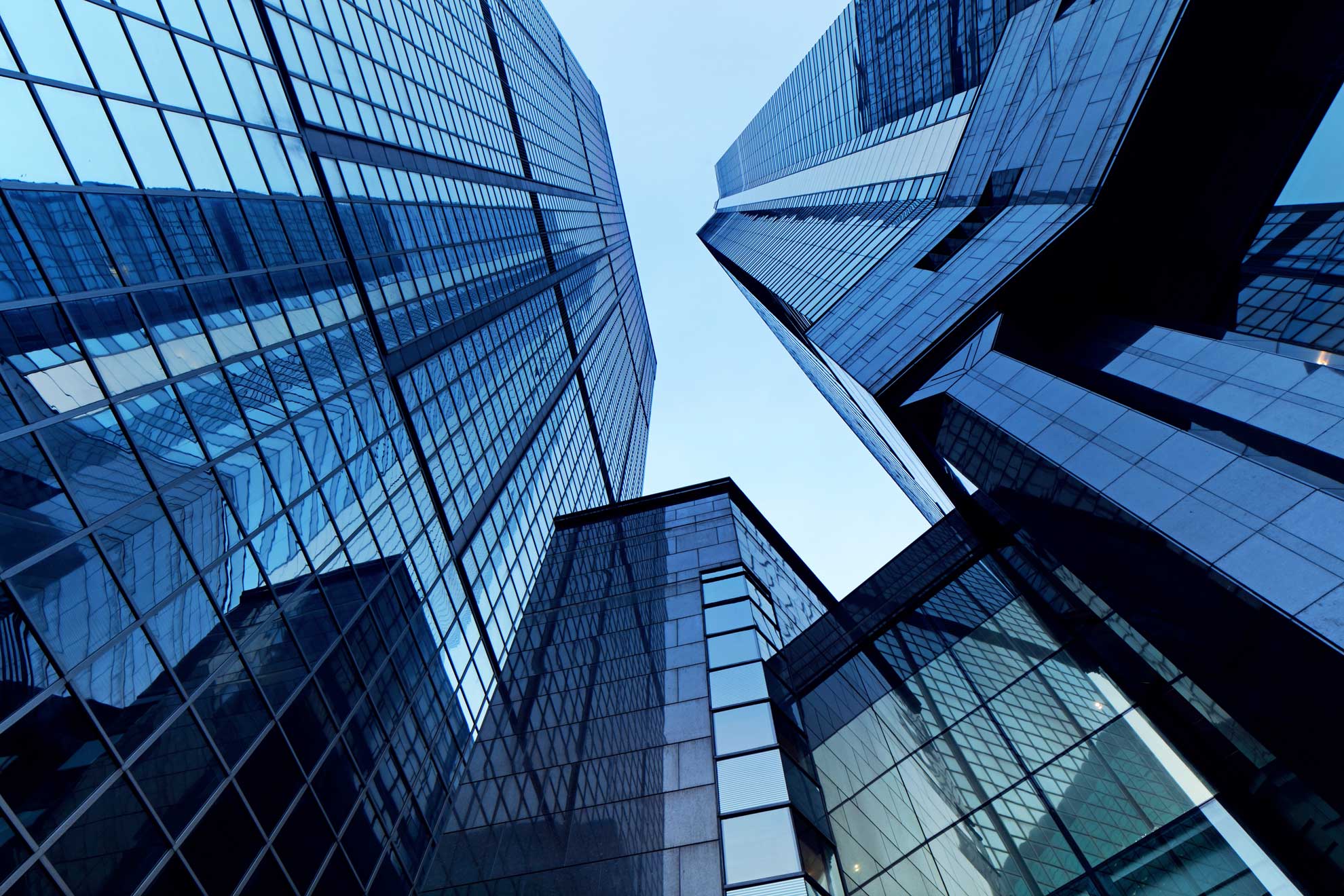
È la capacità di rinnovarsi che determina lo sviluppo e il successo di un'azienda nel tempo.
In questo processo la tecnologia e la digitalizzazione hanno un ruolo essenziale.
Siamo specializzati in strategie di trasformazione digitale per qualsiasi tipo di azienda, supportate da una costante ricerca per l'individuazione di agevolazioni e contributi utili ad ammortizzare gli investimenti effettuati.
Cosa facciamo?
Troviamo soluzioni per favorire la crescita aziendale.
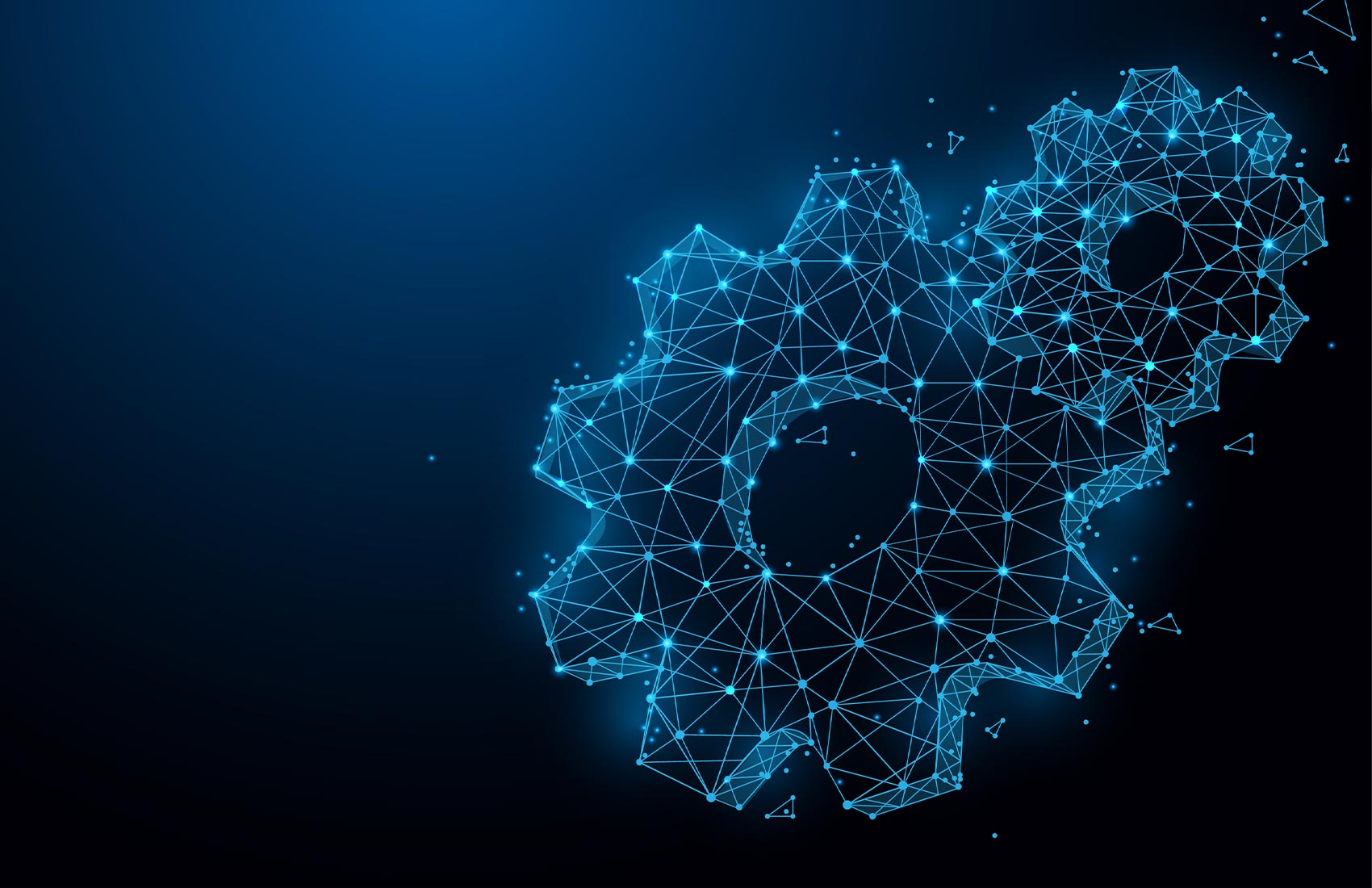
Trasformazione digitale
Analizziamo i processi e implementiamo tecnologie intelligenti per ottimizzarne l'efficienza.
Le nostre tecnologieFinanza agevolata
Otteniamo l'accesso a tutte le agevolazioni pubbliche che supportano lo sviluppo aziendale.
Scopri di più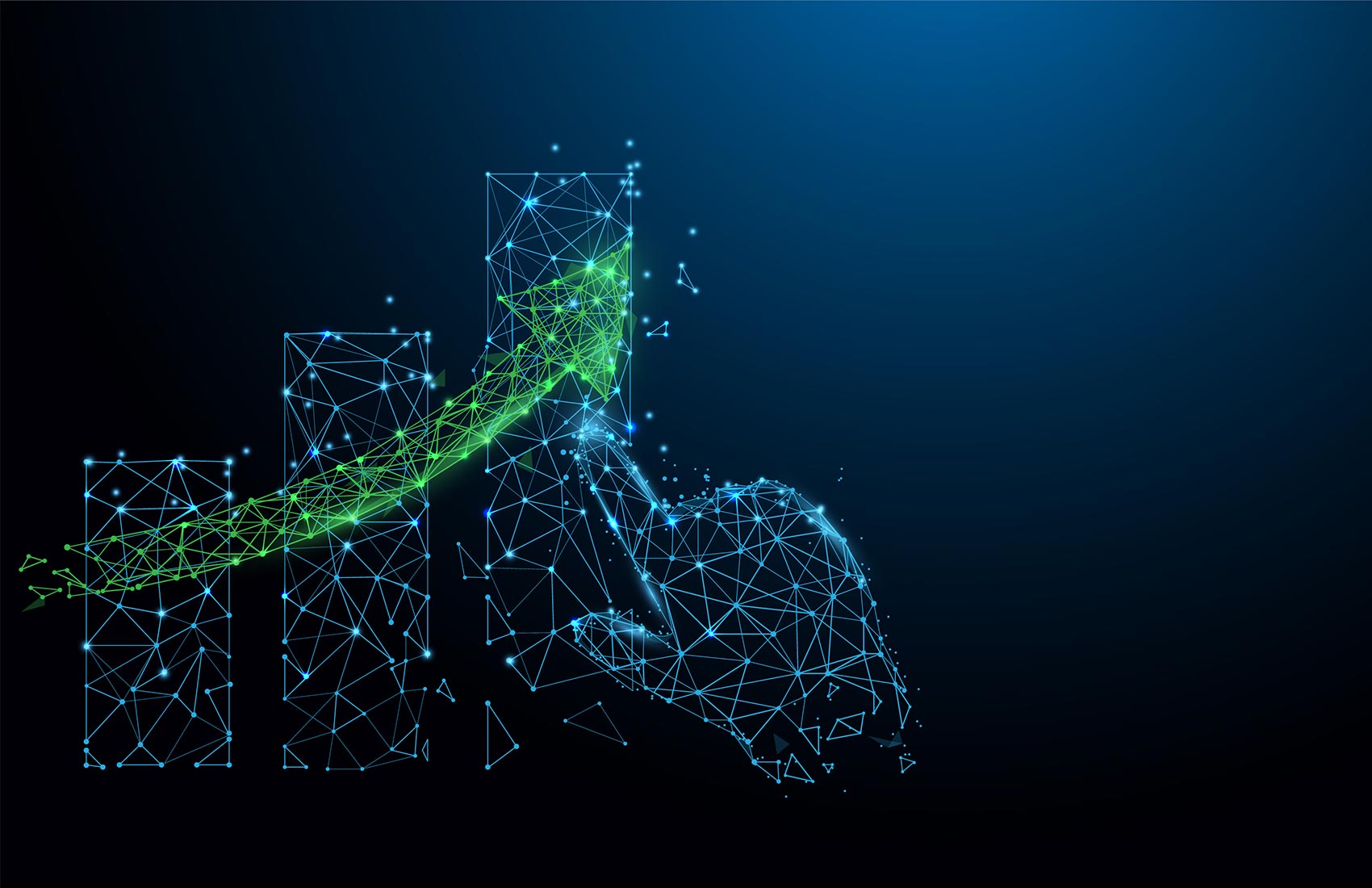
Sviluppiamo tecnologie digitali innovative per accelerare lo sviluppo aziendale
Pianifichiamo la crescita aziendale attraverso l'impiego di tecnologie digitali all'avanguardia e personalizzate, l'installazione di software dedicati, l'implementazione di strategie di digital marketing nazionali ed estere, la visibilità del Brand online.
Questi sono i nostri principali servizi Digital:
Siamo formatori 4.0, con certificazione di qualità ISO 9001.
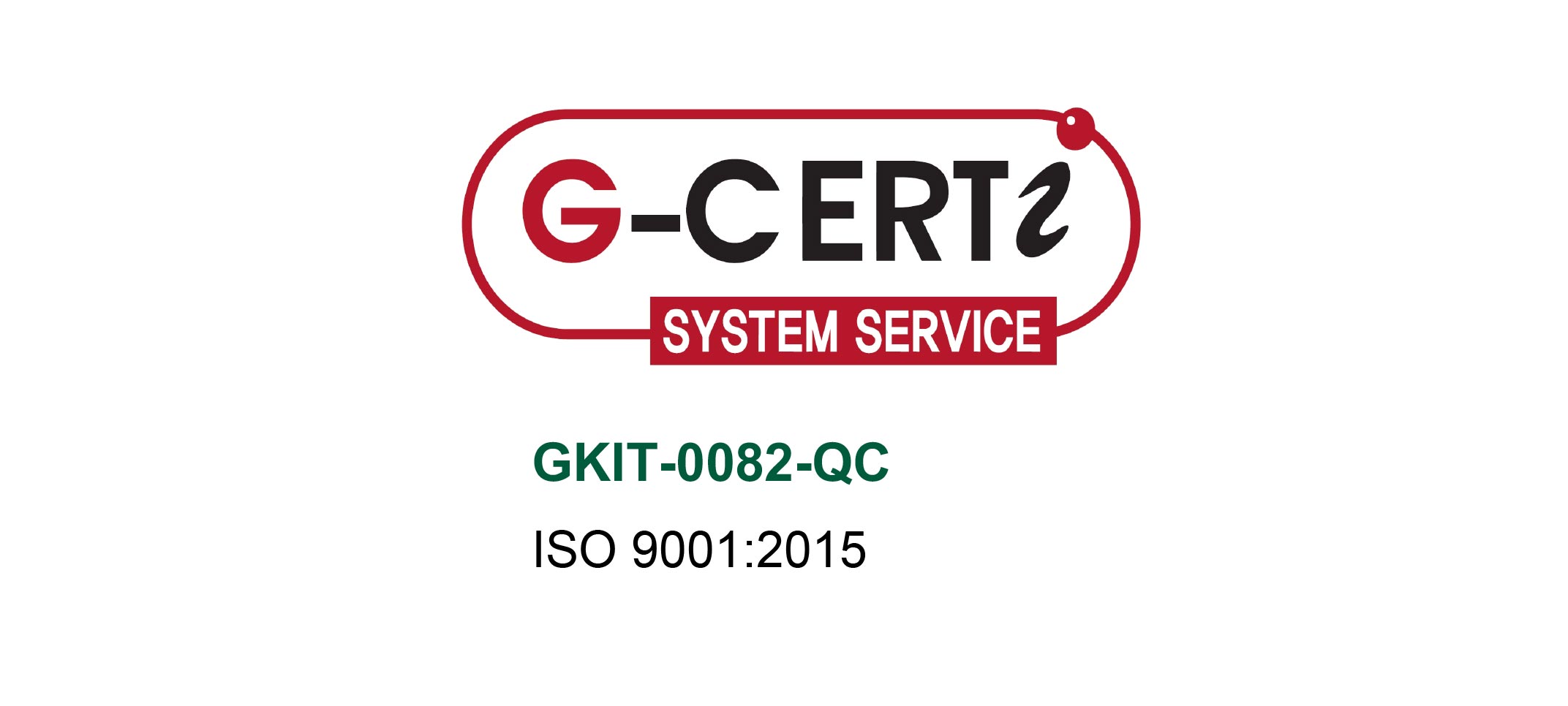
Intercettiamo le agevolazioni pubbliche a sostegno degli investimenti, senza anticipi
Ricerchiamo costantemente agevolazioni pubbliche a supporto degli investimenti effettuati, con l'obiettivo di abbattere gli sforzi economici sostenuti. Offriamo la nostra consulenza senza chiedere alcun anticipo, conseguendo un premio solo a successo finale.
Questi sono i nostri principali servizi Finance:
Tendenze e approfondimenti dal mondo digital e finance
Abbiamo selezionato alcuni articoli che potrebbero essere di tuo interesse.
Vedi tutti gli articoli del nostro blog.
Parlano di noi
In questa sezione troverete dei riferimenti a siti, giornali o altri media che hanno parlato di noi. Una rassegna che permette di scoprire molti dettagli sui servizi e sui prodotti di Glacom, analizzati da professionisti del settore.